Смотровое окно для фреона – Кондиционеры – теория. Фильтр осушитель для компрессора, смотровые стекла. – кондиционеры +7-927-791-01-07, Самара и область
Устройство холодильной машины
Охлаждение различных объектов – продуктов питания, воды, других жидкостей, воздуха, технических газов и др. до температур ниже температуры окружающей среды происходит с помощью холодильных машин различных типов. Холодильная машина по большому счету не производит холод, она является лишь своеобразным насосом, который переносит теплоту от менее нагретых тел к более нагретым. Основан же процесс охлаждения на постоянном повторении т.н. обратного термодинамического или другими словами холодильного цикла. В самом распространенном парокомпрессионном холодильном цикле перенос теплоты происходит при фазовых превращениях хладагента – его испарении (кипении) и конденсации за счет потребления подведенной извне энергии.
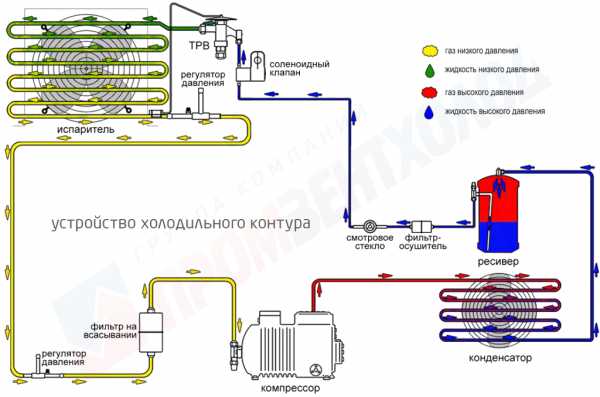
Основными элементами холодильной машины, с помощью которых реализуется ее рабочий цикл, являются:
- компрессор – элемент холодильного цикла, обеспечивающий повышение давления хладагента и его циркуляцию в контуре холодильной машины;
- дросселирующее устройство (капиллярная трубка, терморегулирующий вентиль) служит регулирования количества хладагента, попадающего в испаритель в зависимости от перегрева на испарителе.
- испаритель (охладитель) – теплообменник, в котором происходит кипение хладагента (с поглощением тепла) и непосредственно сам процесс охлаждения;
- конденсатор – теплообменник, в котором в результате фазового перехода хладагента из газообразного состояния в жидкое, отведенная теплота сбрасывается в окружающую среду.
При этом необходимо наличие в холодильной машине других вспомогательных элементов, – электромагнитные (соленоидные) вентили, контрольно-измерительные приборы, смотровые стекла, фильтры-осушители и т.д. Все элементы соединены между собой в герметичный внутренний контур с помощью трубопроводов с теплоизоляцией. Контур холодильной машины заполняется хладагентом в необходимом количестве. Основной энергетической характеристикой холодильной машины является холодильный коэффициент, который определяется отношением количества тепла, отведенного от охлаждаемого источника, к затраченной энергии.
Холодильные машины в зависимости от принципов работы и применяемого хладагента бывают нескольких типов. Наиболее распространенные парокомпрессионные, пароэжекторные, абсорбционные, воздушные и термоэлектрические.
Хладагент
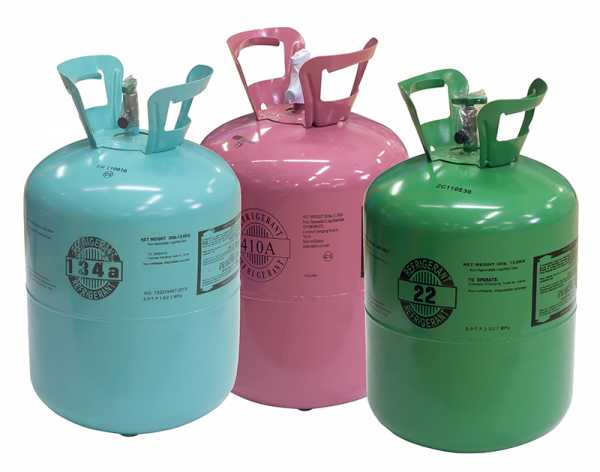
Хладагент – рабочее вещество холодильного цикла, основной характеристикой которого является низкая температура кипения. В качестве хладагентов чаще всего применяют различные углеводородные соединения, которые могут содержать атомы хлора, фтора или брома. Также хладагентом могут быть аммиак, углекислый газ, пропан и т.д. Реже в качестве хладагента применяют воздух. Всего известно около сотни типов хладагентов, но изготавливается промышленным способом и широко применяется в холодильной, криогенной технике, кондиционировании воздуха и других отраслях всего около 40. Это R12, R22, R134A, R407C, R404A, R410A, R717, R507 и другие. Основная область применения хладагентов – это холодильная и химическая промышленность. Кроме того, некоторые фреоны используют в качестве пропеллентов при производстве различной продукции в аэрозольной упаковке; вспенивателей при производстве полиуретановых и теплоизолирующих изделий; растворителей; а также в качестве веществ, тормозящих реакцию горения, для систем пожаротушения различных объектов повышенной опасности – тепловых и атомных электростанций, гражданских морских судов, боевых кораблей и подводных лодок.
Терморегулирующий вентиль (ТРВ)
Терморегулирующий вентиль (ТРВ) – один из основных компонентов холодильных машин, известен как наиболее распространенный элемент для дросселирования и точного регулирования подачи хладагента в испаритель. ТРВ использует в качестве регулятора расхода хладагента клапан игольчатого типа, примыкающий к основанию тарельчатой формы. Количество и расход хладагента определяется проходным сечением ТРВ и зависит от температуры на выходе из испарителя. При изменении температуры хладагента на выходе из испарителя, давление внутри этой системы меняется. При изменении давления меняется проходное сечение ТРВ и, соответственно, меняется расход хладагента.
Термосистема заполнена на заводе-изготовителе точно определенным количеством того же хладагента, который является рабочим веществом данной холодильной машины. Задача ТРВ – дросселирование и регулирование расхода хладагента на входе в испаритель таким образом, чтобы в нем наиболее эффективно проходил процесс охлаждения. При этом хладагент должен полностью перейти в парообразное состояние. Это необходимо для надежной работы компрессора и исключения его работы т.н. «влажным» ходом (т.е. сжатие жидкости). Термобаллон крепится на трубопровод между испарителем и компрессором, причем в месте крепления необходимо обеспечить надежный термический контакт и теплоизоляцию от воздействия температуры окружающей среды. Последние 15-20 лет в холодильной технике стали получать широкое распространение электронные ТРВ. Они отличаются тем, что у них отсутствует выносная термосистема, а ее роль играет терморезистор, закрепленный на трубопроводе за испарителем, связанный кабелем с микропроцессорным контролером, который в свою очередь управляет электронным ТРВ и вообще всеми рабочими процессами холодильной машины.
Соленоидный вентиль
Соленоидный вентиль служит для двухпозиционного регулирования («открыто-закрыто») подачи хладагента в испаритель холодильной машины либо для открытия-закрытия от внешнего сигнала определенных участков трубопроводов. При отсутствии питания на катушке тарелка клапана под воздействием специальной пружины удерживает соленоидный вентиль закрытым. При подаче питания сердечник электромагнита, соединенный штоком с тарелкой, преодолевает усилие пружины, втягивается в катушку, тем самым приподнимая тарелку и открывая проходное сечение вентиля для подачи хладагента.
Смотровое стекло
Смотровое стекло в холодильной машине предназначено для определения:
- состояния хладагента;
- наличие влаги в хладагенте, которое определяется цветом индикатора.
Смотровое стекло обычно монтируют в трубопроводе на выходе из накопительного ресивера. Конструктивно смотровое стекло представляет собой металлический герметичный корпус с окном из прозрачного стекла. Если при работе холодильной машины в окне наблюдается поток жидкости с отдельными пузырями парообразного хладагента, то это может свидетельствовать о недостаточной заправке или других неисправностях в ее функционировании. Может устанавливаться и второе смотровое стекло на другом конце указанного выше трубопровода, в непосредственной близости от регулятора расхода, которым может быть соленоидный вентиль, ТРВ или капиллярная трубка. Цвет индикатора показывает наличие или отсутствие влаги в холодильном контуре.
Фильтр-осушитель
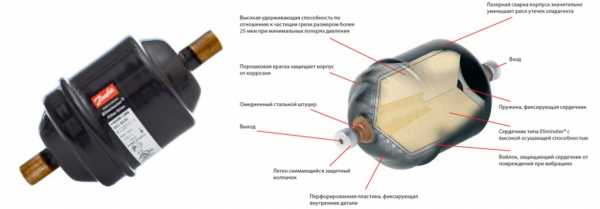
Фильтр-осушитель или цеолитовый патрон еще один важный элемент контура холодильных машин. Он необходим для удаления влаги и механических загрязнений из хладагента, тем самым защищая от засорения ТРВ. Обычно он монтируется с помощью паяных или штуцерных соединений непосредственно в трубопровод между конденсатором и ТРВ (соленоидным вентилем, капиллярной трубкой). Чаще всего конструктивно представляет собой отрезок медной трубы диаметром 16…30 и длиной 90…170 мм, закатанный с обеих сторон и с присоединительными патрубками. Внутри по краям установлены две металлические фильтрующие сетки, между которыми расположен гранулированный (1,5…3,0 мм) адсорбент, обычно это синтетический цеолит. Это т.н. разовый фильтр-осушитель, но существуют многоразовые конструкции фильтров с разборным корпусом и резьбовыми трубопроводными соединениями, требующими только время от времени замены внутреннего цеолитового картриджа. Замена разового фильтра- осушителя или картриджа необходима после каждого вскрытия внутреннего контура холодильной машины. Существуют одно-направленные фильтры, предназначенные для работы в системах «только холод» и дву-направленные, используемые в агрегатах «тепло-холод».
Ресивер
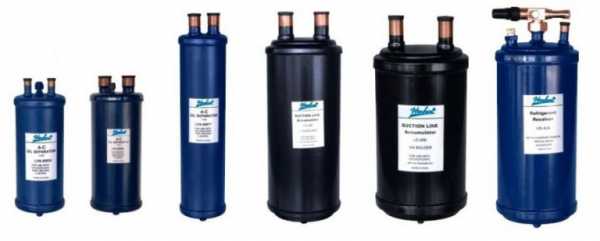
Ресивер – герметичный цилиндрический накопительный бак различной емкости, изготовленный из стального листа, и служащий для сбора жидкого хладагента и его равномерной подачи к регулятору расхода (ТРВ, капиллярная трубка) и в испаритель. Существуют ресиверы как вертикального, так и горизонтального типа. Различают линейные, дренажные, циркуляционные и защитные ресиверы. Линейный ресивер устанавливается с помощью паяных соединений в трубопровод между конденсатором и ТРВ и выполняет следующие функции:
- обеспечивает непрерывную и бесперебойную работу холодильной машины при различных тепловых нагрузках;
- является гидравлическим затвором, препятствующим попаданию пара хладагента в ТРВ;
- выполняет функцию масло- и воздухоотделителя;
- освобождает трубы конденсатора от жидкого хладагента.
Дренажные ресиверы служат для сбора и хранение всего количества заправленного хладагента на время ремонтных и сервисных работ, связанных с разгерметизацией внутреннего контура холодильной машины.
Циркуляционные ресиверы применяют в насосно-циркуляционных схемах подачи жидкого хладагента в испаритель для обеспечения непрерывной работы насоса и монтируют в трубопровод после испарителя в точку с самой низкой отметкой по высоте для свободного слива в него жидкости.
Защитные ресиверы предназначены для безнасосных схем подачи фреона в испаритель, их устанавливают совместно с отделителями жидкости во всасывающий трубопровод между испарителем и компрессором. Они служат для защиты компрессора от возможной работы «влажным» ходом.
Регулятор давления
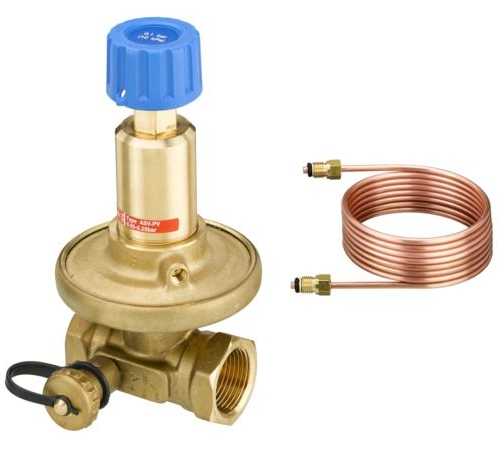
Регулятор давления – автоматически управляемый регулирующий клапан, применяемый для снижения либо поддержания давления хладагента путем изменения гидравлического сопротивления потоку проходящего через него жидкого хладагента. Конструктивно состоит из трех основных элементов: регулирующего клапана, его исполнительного механизма и измерительного элемента. Исполнительный механизм непосредственно воздействует на тарелку клапана, изменяя или закрывая проходное сечение. Измерительный элемент сравнивает текущее и заданное значение давления хладагента и формирует управляющий сигнал для исполнительного механизма регулирующего клапана. В холодильной технике существуют регуляторы низкого давления, чаще называемые прессостатами. Они управляют давлением кипения в испарителе, их устанавливают во всасывающий трубопровод за испарителем. Регуляторы высокого давления называют маноконтроллерами. Их чаще всего применяют в холодильных машинах с воздушным охлаждением конденсатора для поддержания минимально необходимого давления конденсации при понижении температуры наружного воздуха в переходный и холодный период года, обеспечивая тем самым т.н. зимнее регулирование. Маноконтроллер устанавливают в нагнетательный трубопровод между компрессором и конденсатором.
Специалисты рекомендуют
Вернуться
www.promventholod.ru
Влага во фреоновом контуре. Рекомендации по замене фреонового фильтра в промышленном чиллере.
Регламентная замена фреонового фильтра
Регламентная замена фреонового фильтра производится примерно раз в 5 лет, в зависимости от наличия влаги во фреоновом контуре промышленного водоохладителя, попавшей внутрь холодильного контура. Частоту регламентной замены фреонового фильтра определяет производитель чиллера, что и указывает в «Руководстве по эксплуатации», в разделе «Техническое обслуживание» или «Регламентное техническое обслуживание чиллера».
Влага может попадать внутрь фреонового контура по причине не герметичности системы, например, через неплотные резьбовые или вальцованные соединения, микротрещины, и по многим другим причинам. Последствия этого могут быть самыми разными, от ухудшения теплообмена и окисления обмоток компрессора, что может стать причиной его замыкания, до подмерзания ТРВ и электромагнитного клапана и прекращения их нормального функционирования. В любом случае, наличие влаги в контуре пагубно сказываться на работе всего промышленного водоохладителя в целом.
Проблема небольшого количества влаги во фреоновом контре решается путем замены фреонового силикагелевого фильтра, который имеет не только фильтрующий, но и влагозадерживающий эффект. Основное наполнение любого такого фильтра — силикагель, который является абсорбентом влаги.
Ниже приведен пошаговый метод и рекомендации по замене фреонового фильтра.
Рекомендации по замене фреонового фильтра в промышленном чиллере
1. Определение наличия влаги в системе фреонового контура
Наличие влаги определяется по цвету индикатора влажности в смотровом стекле чиллера (см.рис. ниже).
Индикатор влажности, в центре смотрового стекла, должен иметь сплошной зеленый цвет. По окружности смотрового стекла вклеена специальная информационная наклейка, на которой указано какой цвет индикатора, о чем он свидетельствует. На зеленом фоне надпись — DRY, что в переводе в английского языка — «сухо, сухой». Следовательно, если цвет индикатора зеленый, значит влага в системе отсутствует или присутствует в незначительном количестве, которое не определяется индикатором влажности и не является критичным для работы промышленного чиллера.
При наличии на индикаторе влажности значительных желтых вкраплений (более 50% от общей площади индикатора влажности), или же индикатор полностью желтого цвета, руководствуемся информационной наклейкой, на желтом фоне которой надпись — WET что в переводе в английского языка «влажный, мокрый». Делаем вывод, что влага в системе присутствует в существенном количестве и ее необходимо удалить из фреонового контура чиллера.
Рис. 1 Смотровое стекло промышленного чиллера
2. Удаление влаги из фреонового контура
Первое, что необходимо сделать — это найти причину попадания влаги в систему и соответственно ее устранить.
Удаление влаги из фреонового контура может происходить различными способами.
Наиболее эффективным, но наименее распространенным является — стравливание всего объема хладагента из фреонового контура, с последующей сушкой системы азотом, возможна многократная закачка азота в холодильный контур, с различной длительностью. Далее вакуумирование системы в течении длительного времени, сообразного мощности вакуумного насоса и внутреннему объему контура, пока индикатор влажности не станет полностью зеленым. К данному способу прибегают в крайних случая, при очень большом количестве воды в системе (например, при размораживании пластинчатого испарителя в промышленном генераторе ледяной воды и проч.). При малых количества влаги и большой емкости фреона в системе такую операцию производить нецелесообразно, так как это весьма затратно и долго.
Самым распространённым, быстрым и простым способом осушения фреонового контура является — замена силикагелевого фильтра.
Необходимо перекрыть вентиль выхода жидкого хладагента от ресивера к фильтру (рис.2)
.
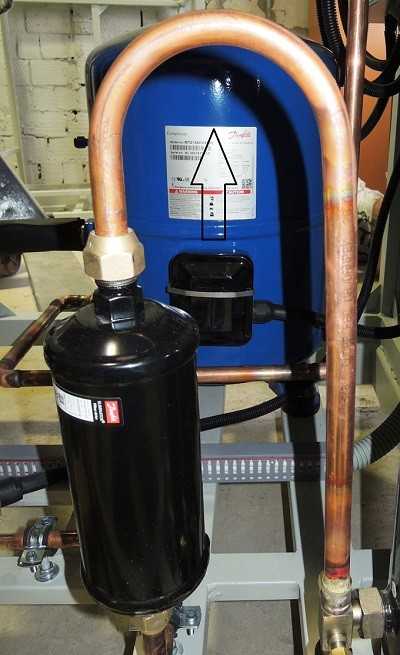
Рис. 2 Фильтр чиллера
Убедиться в отсутствии электропитания на катушке электромагнитного клапана, который открывает подачу жидкого фреона к ТРВ и далее к испарителю — соленоид должен быть закрыт (рис.3).
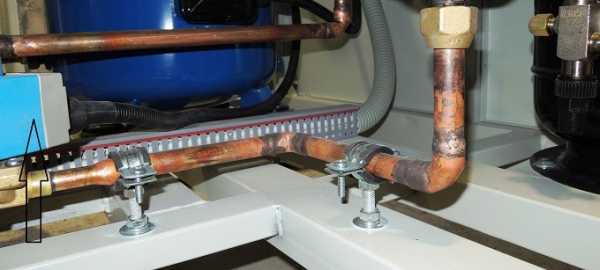
Рис. 3 Соленоид чиллера
Далее необходимо открутить гайки, соединяющие вальцованную трубку к фланцу фильтра.
При откручивании и закручивании гаек на фильтре, предварительно необходимо побрызгать маслом, WD-40 или другим средством подобного действия под медную трубу и резьбу, в местах прилегания гаек — для уменьшения силы трения гайки об трубу, во избежание ее сворачивания в сторону кручения гайки гаечным ключом.
При вальцевании трубы она предварительно повергается нагреву — обжигу. В противном случае, необожжённая медная труба при вальцевании лопнет.
Обожжённая медная труба при внешнем механическом воздействии подвержена деформации. Поэтому, при откручивании и закручивании гаек, необходимо удерживать сам фильтр вторым ключом и прилагать равные усилия в противоположную сторону относительно кручения гаек. Пробрызгивание необходимо производить как при откручивании, так и при закручивании до и после фильтра, независимо от длины трубки. Даже при длинном и изогнутом отрезке необожжённой трубы после места обжига, при отсутствии смазки, неизбежен загиб или залом трубки, по причине того, что крутящие усилие распространяется равномерно по всей прямой длине трубы, а наиболее слабый участок, вне зависимости от места приложения усилия подвергнется деформации, что может повлечь появления микротрещин и разрыва поверхности трубы (Рис.4).
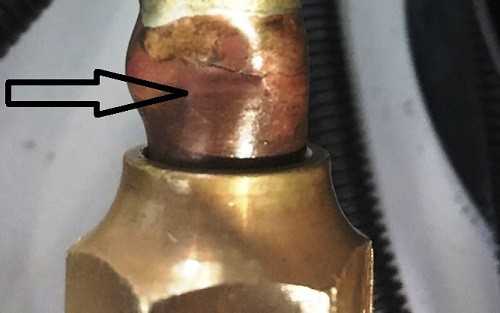
Рис. 4 Гайка фильтра чиллера
Если есть возможность, то будет уместным аккуратное придерживание обожжённого участка трубки трубным ключом с прорезиненными губцами или ремешковым трубным ключом (рис. 5).
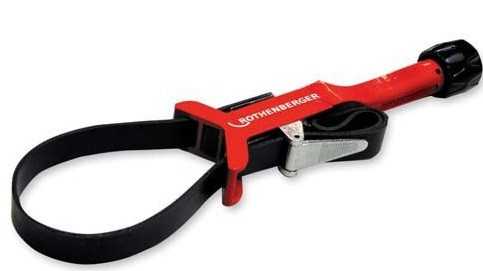
Рис. 5. Трубный ключ для медных трубок чиллера
Основная фиксация трубки ключом должна осуществляться не за счет прижима трубки губцами или сильной затяжки резинового ремешка, а преимущественно за счет крутящей силы трения трубки об мягкую резину губцов трубного ключа или силиконового ремешка. Перед закручиванием гаек на фильтре, нанести на резьбу фильтра резьбовой клей — в качестве фиксации и предотвращения от раскручивания гаек, при вибрации.
Далее, при наличи клапана Шредера в фильтре (см. рис. 6) или на участке от выходного вентиля ресивера до соленоида, произвести вакуумирование, открыть вентиль ресивера, произвести запуск установки.
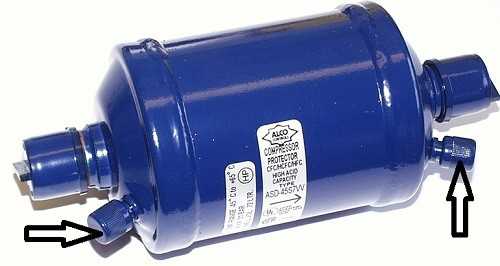
Рис. 6. Фильтр с клапаном для чиллера
При отсутствии клапана Шредера — закрутить гайки, но не затягивать, подать питание на катушку электромагнитного клапана, оставшийся в испарителе фреон, под избыточным (относительно атмосферного) давлением воздух выдавит из завоздушенного участка, далее затянуть гайки, как описано выше.
После запуска промышленного чиллера, дайте ему поработать в режиме некоторое время (обычно сутки) и посмотрите цвет индикатора влажности. Если цвет зеленый, следовательно, вся влага была абсорбирована фильтром. Если цвет желтый или имеются желтые вкрапления (более 50% площади индикатора), то необходимо провести повторную замену фильтра, вероятно количество влаги в системе превзошло абсорбирующие возможности фильтра. Далее вмонтировать новый фильтр и повторить «эксперимент».
Как правило, при небольшом количестве влаги 1-2 замен фильтра оказываться достаточно. При попадании большого количества воды, придется воспользоваться первым способом, на практике, третий раз менять фильтр, оказывается нецелесообразно.
У некоторых профессионалов для целей сбора влаги из системы используются гибкие шланги, для временного включение в любой фреоновый контур выносного (внешнего) фильтра. Как правило, эти внешние фильтры имеют больший объем по производительности, относительно существующего фреонового контура, для более быстрого и эффективного сбора влаги, а также сменные силикагелевые вставки, которые меняются в стальном корпусе фильтра, что удешевляет процедуру осушения, так как не приходится выбрасывать фильтр целиком. А уже по достижении зеленого цвета индикатора влажности в смотровом стекле промышленного водоохладителя — устанавливают новый, штатный фильтр.
Замена фреонового фильтра в промышленном чиллере должна осуществляться только специалистом по холодильной технике, с соблюдением всех необходимых правил. Это связано с тем, что данная техника содержит вещества, которые разрушают озоновый слой и влияют на ухудшение экологии.
cp-h.ru
Кондиционеры – теория. Фильтр осушитель для компрессора, смотровые стекла. – кондиционеры +7-927-791-01-07, Самара и область
Кондиционер. Фильтр осушитель для компрессора и холодильного оборудования, смотровые стекла. Учебный курс. Теоретические основы.
Что такое Фильтр – осушитель, применяемый для кондиционера или холодильного оборудования? Фильтр – осушитель представляет собой устройство, которое удаляет посторонние твердые частицы (грязь), влагу, кислоты, которые могли бы повлиять на нормальный рабочий режим системы охлаждения, а зачастую постепенно привести к выходу всей системы из строя.используется в приборах: холодильник, бытовой холодильник, кондиционер, холодильная витрина и т.д.![]() |
Для чего нужен фильтр осушитель в холодильной системе?
Фильтр осушитель используется для защиты холодильных машин – от посторонних частиц.
Фильтр осушитель – минимизирует химические реакции в системе путем удаления посторонних частиц |
![]() |
Фильтр осушитель – предотвращает образование льда в термо регулирующем вентиле (капиллярная трубка), путем удаления частиц воды, из хладагента.
Фильтр осушитель, также может удалить другие загрязняющие вещества: твердые ржавые материалы и кислоты. |
![]() |
Фильтр-осушитель обычно устанавливают на линии жидкости перед терморегулирующим вентилем для защиты его от воды и грязи.Скорость хладагента в жидкостной линии невысока, и поэтому контакт между хладагентом и твердым сердечником фильтра-осушителя достаточно хороший. В то же время гидравлическое сопротивление фильтра незначительно. Фильтры, устанавливаемые во всасывающем трубопроводе, так называемые «антикислотные» фильтры, применяются для удаления кислот из системы после выхода двигателя компрессора из строя в результате пережога. Для того, чтобы падение давления на фильтре было небольшим, фильтр, устанавливаемый на линии всасывания, должен быть больше фильтра, устанавливаемого в жидкостной линии. Фильтр на линии всасывания должен заменяться новым при падении давления на фильтре, превышающем следующие значения: В системах кондиционирования (А/С): 0,50 бар В холодильных установках: 0,25 бар В морозильных установках: 0,15 бар. |
Стандартные фильтры-осушители:
![]() |
При установке фильтра направление стрелки на его этикетке должно совпадать с направлением движения хладагента в магистрали. |
Типы фильтров – осушителей.
![]() |
• Фильтр жидкостной линии (Liquid line)
• Фильтр линии всасывания (suction line) |
Фильтр – осушитель. Конструкция.
Типы присоединения (штуцеры) :
Твердый сердечник.
![]() |
Твердый сердечник обладает большими возможностями для поглощения воды и сохранения накопленной влаги. Молекулярное сито задерживает воду, а активированная окись алюминия — воду и кислоты. Твердый сердечник совместно с полиэфирной сеткой действуют как фильтр для задержки грязи. В твердом сердечнике задерживаются крупные частицы грязи, в полиэфирной сетке – более мелкие частицы. Фильтр-осушитель способен задерживать все частицы, размеры которых превышают 25 микрон. |
Холодильные системы (refrigeration system). Образование кислоты, клин компрессора.
(описан принцип разложения фреона (хладагента, причины образования кислоты, и причины клина (заклинивания компрессора кондиционера)
Следующие элементы – все это присутствует в системе охлаждения:
хладагент
кислород
метал оксиды
загрязняющие
осушители |
![]() |
масло
вода
продукты коррозии
температура
каталитическая |
расширительный вентиль (expansion valve)
испаритель (evaporator)
компрессор (compressor)
фильтр осушитель (filter drier)
конденсатор (condenser)
Хладагент.
Разложение хладагента может произойти из-за следующих факторов:
температура, химическая нестабильность, каталитическая активность, вода, кислород.
Основные причины образования кислот при высокой температуре в компрессоре.
Хладагент – образование кислоты.
Образование кислоты может происходить внутри холодильной системы в связи с разложением хладагента или другого вещества в системе.
Два типа кислоты может быть образовано внутри холодильной системы:
1. Неорганические кислоты (inorganic acids) – от разложения хладагента, который содержит хлор (Cl) и фтор (F).
2. Органические кислоты (organic acids) – от разложения нефти (минеральное или полиэфирное масло)
Хладагент и неорганические кислоты.
HCL – хлористый водород H2O – вода H3O – гидроний (комплексный ион, соединение CL – хлор |
неорганические кислоты могут быть получены из разложения хладагента или фреона (т.е. хлора и фтора).Ниже приведены факторы, влияющие на скорость разложения хладагента: • Температура • Содержание кислорода • Содержание воды • Каталитическая активность • Химическая стабильность хладагентаЕсли какой-либо из перечисленных выше факторов сведен к минимуму, хладагент будет оставаться более менее стабильным даже при более высоким уровне влияния остальных факторов. • Например, если температура, вода и каталитическая активность минимальны, то более высокий уровень кислорода может быть допустим и не приведет к разложению хладагента. |
Хладагент и органическая кислота
Органические кислоты могут быть получены путем разложения минерального масло или полиэфирного масла.
![]() |
• Минеральное масло – Органические кислоты образуются из минерального масла, в результате термических или механических нагрузок. Эти кислоты с очень высокой кислотностью.
|
Осушитель.
![]() |
• Активированный оксид алюминия и молекулярное сито используются в качестве осушителей. |
Как работает осушитель?
Важно понять как осушитель адсорбирует влагу.
(Справочно: Адсорбцией называется процесс разделения, основанный на поглощении газов или паров из газовых смесей или растворенных веществ из растворов твердыми пористыми поглотителями.
Твердый пористый поглотитель называется адсорбентом, поглощаемое вещество – адсорбтивом.
Явление адсорбции объясняется наличием притяжения между молекулами адсорбента и адсорбтива. Оказывается, что на границе раздела фаз действуют неодинаковые силы притяжения со стороны молекул носителя и адсорбента. Молекулы адсорбтива, переходя на поверхность адсорбента, уменьшают ее свободную энергию, в результате чего выделяется тепло.
Силы притяжения со стороны адсорбента могут быть либо физическими (Ван-дер Ваальсовы) или химическими. Соответственно этому различают адсорбцию физическую или химическую.
При физической адсорбции выделяется незначительное количество теплоты. Физическая адсорбция обратима (десорбция). После химической адсорбции обратимый процесс практически неосуществим.
Разновидностью адсорбции является капиллярная конденсация. Капиллярная конденсация зависит от связей вещества, находящихся на поверхности твердого поглотителя в жидком состоянии.
Если жидкость смачивает поверхность адсорбента, то происходит конденсация пара с заполнением объема капилляров этой жидкостью. Явление капиллярной конденсации основано на понижении давления pнас над вогнутой поверхностью жидкости в капилляре. Перечисленные виды адсорбции сопутствуют друг другу)
Адсорбция воды представляет собой комбинированный результат из трех явлений:
1. Хемосорбция (химическая адсорбция)
2. физической адсорбции (Физическая адсорбция)
3. Капиллярная конденсация
Молекулярное сито – цеолит.
![]() |
Цеолиты – чрезвычайно важный класс неорганических материалов, которые могут отделить газы или жидкости на основе их молекулярного размера и формы. Поры молекулярного сита обладают способностью захватывать молекулы воды. Но если воды в газе нет, то в них могут заходить и удерживаться другие молекулы. Правда, если в отверстие обычного сита проходят мелкие частицы, а более крупные удерживаются в нем, то здесь, в необычайно пористом молекулярном веществе, наоборот, крупные молекулы проходят мимо сита, а мелкие застревают. Естественно, что в зависимости от величины и химической природы молекул, которые должны быть отсеяны от смеси газов, изготавливаются сита различного физического и химического характера как для больших, так и для малых молекул. • Цеолит представляет собой тип молекулярного сита. • Он обладает способностью избирательно сортировать молекулы, основываясь, прежде всего, на размере молекул. Это связано с его пористой структурой; причем поры – молекулярных размеров. Макро каналы ведут в микро полости которые адсорбирует молекулы воды. |
Размер молекул различных хладогентов.
Молекулярные размеры цеолита и различных хладагентов приведены ниже.
Осушители должны ставиться в правильно спроектированную систему, содержащими достаточное количество влагопоглотителя соответствующего типа и приемлемого качества. Содержание влаги в хладагенте должно быть не более 10 промилле (ppm, 1 ppp=10 -6 ). Предельно допустимое содержание влаги составляет 20 ppm.
Размер молекулы воды составляет 2,8 Ангстрем (А). Следовательно, в системы с обычно используемыми хладагентами можно устанавливать осушители из материала типа «молекулярное сито» с размером пор около 3 А.
При каких условиях влага может попасть в систему охлаждения?
![]() |
когда система охлаждения монтируется, строится
когда система охлаждения находиться вскрытой для обслуживания
когда утечка находиться на стороне всасывания, в процессе вакуумирования системы
когда есть утечка в охлаждаемом водой конденсаторе
когда система заполняется маслом или хладагентом, содержащие влагу |
Что происходит, когда влага попадает в систему?
Влага в системе охлаждения может привести к:
![]() |
Закупорка расширительного устройства из-за образования льда
Коррозия металлических деталей
химическое повреждение изоляции компрессоров
разрушение или разложение масла (образование кислоты) |
Применение типа осушителя.
![]() |
• Тип осушителя зависит от типа масла и хладагента, используемого в системе.
• в системе с минеральными маслами, фильтр должен содержать активированный оксид алюминия с высокой адсорбционной емкостью для полярных веществ. Оксид алюминия будет действовать для селективной адсорбции и удаления молекул органических кислот.
• В системах с применением полиэфирного масла, выбирают фильтр-осушитель, который эффективно задерживает молекулы воды. |
Смотровые стекла.
![]() |
Смотровые стекла с индикатором влажности устанавливаются: после фильтра осушителя:
по цвету его индикатора влажности можно определить следующее:
По наличию пузырей в смотровом стекле можно определить: |
![]() |
При установке фильтра направление стрелки на его этикетке должно совпадать с направлением течения хладагента в магистрали. Фильтр осушитель может иметь различную ориентацию в пространстве, но при этом необходимо учитывать следующее: вертикальный монтаж с нисходящим потоком хладагента позволяет осуществлять быстрое опорожнение/вакуумирование холодильной системы; вертикальный монтаж с восходящим потоком хладагента увеличивает время опорожнения/вакуумирования холодильной системы, поскольку хладагент должен испариться из фильтра-осушителя. Сердечник фильтра прочно закреплен в корпусе фильтра. Фильтры-осушители компании Данфосс способны противостоять вибрациям до 10 g*. Убедитесь, что трубы достаточно прочно удерживают фильтр и защищают его от воздействия вибрации. В противном случае закрепите фильтр хомутом или просто установите его в более безопасное место. *10 g — десятикратное значение силы притяжения Земли.Фильтры типа DCR (с заменяемым твердым сердечником) устанавливаются таким образом, чтобы входной штуцер был направлен вверх или горизонтально. Такой монтаж позволяет легко удалять грязь из кожуха при замене сердечника. При монтаже нового фильтра DCR оставляйте место, достаточное для замены сердечника.Не распаковывайте фильтры-осушители или сердечники, если они не предназначены для непосредственного монтажа. Запакованные фильтры лучше сохраняются.Не вакуумируйте и не храните фильтры при избыточном давлении.Пластиковые гайки, установленные на соединительных штуцерах, обеспечивают полную герметичность и гарантируют сухость содержимого фильтра. |
Когда нужно менять фильтр – осушитель.
если смотровое стекло показывает, что содержание влаги слишком высоко (желтый цвет индикатора) | |
Если падение давления на фильтре слишком велико (пузыри в смотровом стекле) | |
после заменены компрессора | |
Каждый раз, когда система охлаждения вскрывалась по разным причинам (замена ТРВ и т.д.) |
Резюме:
• Фильтр-осушитель представляет собой устройство, которое удаляет нежелательные материалы и содержание влаги, которые могут повлиять на оптимальную работу системы охлаждения.
• Есть ре-дизайн фильтры и оригинальные фильтры.
• Фильтры-осушители могут быть установлены на линии жидкости и / или линии всасывания системы охлаждения.
• формирование кислоты в холодильной системе может произойти из-за влажности в хладагенте или масла.
• Фильтр-осушитель содержит сердечник – осушитель, гигроскопичное вещество, которое адсорбирует влагу из хладагента.
• Активированный оксид алюминия и молекулярные сита обычно используются в качестве осушителей.
• Цеолит представляет собой тип молекулярного сита, которые используют в качестве сердечника фильтр-осушителя.
• Тип осушитель выбирают в зависимости от смазочного масла и хладагента, используемого в системе.
• Смотровое стекло указывает на норму или недостаток количества хладагента, и позволяет обнаружить присутствие влаги в хладагенте.
• Смотровое стекло обычно устанавливается после фильтра-осушителя.
• Фильтр-осушитель должен быть заменен:
• Если индикатор смотрового стекла желтый
• Если есть пузырьки в смотровом стекле при нормальной эксплуатации
• Если один из основных компонентов в системе охлаждения был заменен
• Когда система охлаждения была открыта для обслуживания или замены компонентов
bon-nix.ru
5.16. Система кондиционирования воздуха
5.16. Система кондиционирования воздуха
ОБЩИЕ СВЕДЕНИЯ |
Расположение основных узлов системы кондиционирования воздуха
![]() |
1 – конденсатор; 2 – компрессор; 3 – ресивер; 4 – испаритель; 5 – клапан |
Расположение смотрового окна для определения уровня хладагента в системе кондиционирования воздуха
Система кондиционирования воздуха состоит из конденсатора, установленного перед радиатором, испарителя, расположенного около отопителя, компрессора, установленного на двигателе, и дегидратора. Вентилятор отопителя прогоняет теплый воздух в салон автомобиля через испаритель, охлаждает его до требуемой температуры.
Предупреждения
Система кондиционирования воздуха находится под давлением, поэтому нельзя ослаблять никакие соединения в системе кондиционирования, пока не снято давление. Источником повышенной опасности при неправильном обслуживании системы неподготовленным техническим персоналом и при использовании ненадлежащего оборудования является высокое давление и химическое воздействие хладагента.
Система кондиционирования должна обслуживаться исключительно подготовленным техническим персоналом, обученным безопасным приемам работы с применением надлежащего оборудования, с соблюдением правил разгерметизации, ознакомленному с приемами сбора и порядком хранения автомобильного хладагента.
Не допускайте контакта хладагента с кожей.
При работе рядом с системой кондиционирования надевайте защитные очки.
При попадании хладагента на кожу или глаза не растирайте пораженное место. Немедленно промойте холодной водой в течение не менее 15 минут. Немедленно обратитесь к врачу или лечебное учреждение. Самолечение не допускается.
В новом баллоне хладагент находится под давлением. Хранить при температуре не выше 50˚ С. Принимайте меры, исключающие падение баллона с высоты или иные ситуации, которые могут привести к его повреждению.
Работы следует проводить в хорошо вентилируемом помещении. Хладагент быстро испаряется, приводит к уменьшению доступа кислорода и к затрудненному дыханию.
Газообразный
хладагент тяжелее воздуха и сравнительно быстро должен собираться внизу, например,
под автомобилем.
При сгорании хладагента образуется ядовитый газ. Храните хладагент вдали от открытых источников огня. Не курите. При использовании пламенных течеискателей избегайте вдыхания дыма.
При проведении сварочных работ вблизи системы кондицио нирования всегда удаляйте из нее хладагент. Электросварка вблизи трубопроводов с хладагентом может вызвать разложение хладагента под действием ультрафиолетового излучения.Не подвергайте детали системы кондиционирования воздействию высокой температуры или открытого пламени. Перегрев может привести к повышению давления в системе и воспламенению.
Очистка конденсатора или испарителя с помощью водяного пара не допускается. Следует использовать только холодную воду или сжатый воздух.
В системе кондиционирования предусмотрено смотровое окно, предназначенное для грубой оценки уровня заправленного хладагента (см. рис. Расположение смотрового окна для определения уровня хладагента в системе кондиционирования воздуха).
Для проверки уровня хладагента запустите двигатель и включите кондиционер. При работающем компрессоре в смотровом окне не должно наблюдаться пузырьков. Присутствие пузырьков хотя бы и на короткий промежуток времени свидетельству ет о недостаточной заправке хладагента. Появление признаков вспенивания на внутренней стороне смотрового стекла может указывать почти полное отсутствие хладагента. Для полного восстановления работоспособности системы кондиционирова ния магистраль системы должна откачиваться, проверяться на герметичность и заправляться подготовленным персоналом с использованием надлежащего оборудования.
carmanz.com
Проверка уровня хладагента через смотровое окно Mitsubishi Carisma
- Руководства по ремонту
- Руководство по ремонту Митсубиси Каризма 1995-2004 г.в.
- Проверка уровня хладагента через смотровое окно
![]() | Рис. 18.1. Расположение смотрового окна (1) для проверки уровня хладагента |
Смотровое окно является индикатором уровня хладагента в системе кондиционирования. Для проверки уровня очистите стекло и пустите двигатель ( рис. 18.1 ). Нажмите кнопку включения компрессора кондиционера, установите переключатель вентилятора в положение максимальной скорости, а ручку регулировки температуры воздуха передвиньте в положение максимального охлаждения. Через несколько минут работы кондиционера в этом режиме посмотрите на смотровое стекло.
Если смотровое стекло чистое, электромагнитная муфта компрессора включена, линия высокого давления (отводящий шланг компрессора) холодная, а линия низкого давления (подводящий к компрессору шланг) теплая, то система заполнена хладагентом полностью.
Если смотровое стекло чистое, электромагнитная муфта включена, однако не наблюдается значительной разницы температур между линиями высокого и низкого давления (т.е. отводящим от компрессора шлангом и подводящим к компрессору шлангом), то из системы улетучилась часть хладагента.
Если в смотровом стекле видны пена или пузырьки, то это может указывать на недостаточное количество хладагента. Система нуждается в дозаправке хладагентом.
Скачать информацию со страницы↓ Комментарии ↓
1. Эксплуатация автомобиля
1.0 Эксплуатация автомобиля
1.1 Ключи
1.2 Места управления запиранием и отпиранием автомобиля
1.3 Электрические стеклоподъемники
1.4 Подъемно-сдвижной люк крыши
1.5 Сиденья
1.6 Контрольно-измерительные приборы и органы управления
1.7 Переключатель освещения, света фар и указателей поворота
1.8 Переключатель корректора света фар
1.9 Переключатель очистителя и омывателя ветрового стекла
2. Техническое обслуживание
2.0 Техническое обслуживание
2.1 Технические характеристики и данные
2.2 Общие сведения
2.3 Моторное масло
2.4 Замена моторного масла
2.5 Замена масляного фильтра
2.6 Рабочая жидкость для автоматической коробки передач (ATF)
2.7 Охлаждающая жидкость
2.8 Аккумуляторная батарея
2.9 Тормозная жидкость
3. Бензиновые двигатели 4G9
3.0 Бензиновые двигатели 4G9
3.1 Технические характеристики и данные
3.2 Изменения в двигателях 4G92 (модель 6В) с 1997 г.
3.3 Основные данные для регулировок и контроля на двигателях 4G92 (модель 6В)
3.4 Основные данные для регулировок и контроля
3.5 Проверка и регулировка натяжения ремня привода генератора
3.6 Изменения в двигателях 4G92-МР1 с 2001 г.
3.7 Смазочные материалы
3.8 Проверка и регулировка натяжения ремня привода насоса усилителя рулевого управленияя и компрессора кондиционера
3.9 Проверка и регулировка зазоров в приводе клапанов (SOHC)
4. Дизельные двигатели FBQT
4.0 Дизельные двигатели FBQT
4.1 Технические характеристики и данные
4.2 Смазочные материалы
4.3 Проверка и регулировка ремня привода вспомогательных агрегатов (автомобили с кондиционером)
4.4 Проверка и регулировка зазоров клапанов
4.5 Проверка и регулировка момента впрыска топлива
4.6 Проверка и регулировка частоты вращения коленчатого вала двигателя на холостом ходу
4.7 Проверка и регулировка повышенной частоты вращения коленчатого вала двигателя на холостом ходу при прогреве двигателя
4.8 Проверка компрессии
4.9 Регулировка натяжения ремня привода газораспределительного механизма
5. Дизельные двигатели F9Q
5.0 Дизельные двигатели F9Q
5.1 Технические характеристики и данные
5.2 Проверка и регулировка зазоров клапанов
5.3 Проверка частоты вращения коленчатого вала двигателя на холостом ходу
5.4 Проверка компрессии
5.5 Регулировка натяжения ремня привода газораспределительного механизма
5.6 Шкив коленчатого вала
5.7 Распределительный вал и сальник распределительного вала
5.8 Поддон картера двигателя
5.9 Сальники коленчатого вала
6. Система охлаждения
6.0 Система охлаждения
6.1 Технические характеристики и данные
6.2 Общие сведения
6.3 Проверка герметичности системы охлаждения
6.4 Проверка давления открытия клапана крышки радиатора
6.5 Замена охлаждающей жидкости
6.6 Термостат
6.7 Водяной насос
6.8 Шланги и труба системы охлаждения
6.9 Радиатор
7. Система распределенного впрыска (MPI)
7.0 Система распределенного впрыска (MPI)
7.1 Технические характеристики и данные
7.2 Общие сведения
7.3 Функция самодиагностики
7.4 Контрольная лампа индикации неисправности двигателя
7.5 Очистка корпуса дроссельного узла
7.6 Регулировка датчика-выключателя полностью закрытого положения дроссельной заслонки и датчика положения дроссельной заслонки (TPS) автомобилей без системы TCL
7.7 Регулировка датчика-выключателя полностью закрытого положения дроссельной заслонки и датчика положения педали акселератора автомобилей с системой TCL
7.8 Регулировка положения винта-упора рычага дроссельной заслонки (Fixed SAS)
7.9 Регулировка базовой частоты вращения коленчатого вала двигателя на холостом ходу
8. Система непосред-ственного впрыска топлива (GDI)
8.0 Система непосред-ственного впрыска топлива (GDI)
8.1 Технические данные и характеристики
8.2 Общие сведения
8.3 Контрольная лампа индикации неисправностей двигателя («CHECK ENGINE»)
8.4 Снятие давления в системе питания
8.5 Проверка работы топливного насоса низкого давления
8.6 Очистка корпуса дроссельного узла
8.7 Измерение низкого давления топлива между топливными насосами низкого и высокого давления
8.8 Измерение давления топлива на линии между топливным насосом высокого давления и форсунками
8.9 Проверка герметичности системы питания
9. Электрическое оборудование двигателя
9.0 Электрическое оборудование двигателя
9.1 Технические характеристики и данные
9.2 Общие сведения
9.3 Проверка падения выходного напряжения генератора
9.4 Проверка тока отдачи генератора
9.5 Проверка регулятора напряжения
9.6 Генератор
9.7 Стартер
9.8 Стартер с прямой передачей
9.9 Стартер с понижающей передачей
10. Сцепление
10.0 Сцепление
10.1 Технические характеристики и данные
10.2 Общие сведения
10.3 Проверка и регулировка педали сцепления
10.4 Удаление воздуха из гидравлического привода сцепления
10.5 Педаль сцепления
10.6 Проверка датчика выключения сцепления
10.7 Гидравлический привод сцепления автомобилей с бензиновыми двигателями
10.8 Гидравлический привод сцепления автомобилей с дизельными двигателями
10.9 Главный цилиндр гидравлического привода сцепления автомобилей с бензиновыми двигателями
11. Механическая коробка передач
11.0 Механическая коробка передач
11.1 Технические характеристики и данные
11.2 Общие сведения
11.3 Проверка уровня масла
11.4 Замена масла в коробке передач
11.5 Проверка работы механизма блокировки включения передачи заднего хода
11.6 Замена троса привода спидометра
11.7 Механизм переключения передач
11.8 Рычаг переключения передач
11.9 Разборка и сборка рычага переключения передач
12. Автоматическая корбка передач
12.0 Автоматическая корбка передач
12.1 Технические характеристики и данные
12.2 Общие сведения
12.3 Проверка уровня рабочей жидкости в коробке передач
12.4 Замена рабочей жидкости
12.5 Замена масляного фильтра
12.6 Проверка механизма блокировки стартера
12.7 Проверка механизма блокировки переключения режимов АКП
12.8 Регулировка троса селектора
12.9 Регулировка переключателя селектора и троса механизма управления
13. Рулевое управление
13.0 Рулевое управление
13.1 Технические характеристики и данные
13.2 Общие сведения
13.3 Проверка люфта рулевого колеса
13.4 Проверка момента, который необходимо приложить для начала вращения шарового шарнира наконечника рулевой тяги
13.5 Проверка усилия, которое необходимо приложить для поворота рулевого колеса на неподвижном автомобиле
13.6 Проверка самостоятельного возврата рулевого колеса в среднее положение
13.7 Замена жидкости
13.8 Удаление воздуха из гидравлической системы усилителя рулевого управления
13.9 Проверка давления, создаваемого насосом усилителя рулевого управления
14. Тормозная система
14.0 Тормозная система
14.1 Технические характеристики и данные
14.2 Общие сведения
14.3 Проверка и регулировка педали тормоза
14.4 Проверка выключателя стоп-сигналов
14.5 Проверка работоспособности вакуумного усилителя тормозов
14.6 Проверка работоспособности обратного клапана вакуумного усилителя тормозов
14.7 Проверка работоспособности регулятора давления задних тормозов
14.8 Проверка датчика уровня тормозной жидкости
14.9 Удаление воздуха из гидравлического привода тормозов
15. Передняя подвеска и валы привода колес
15.0 Передняя подвеска и валы привода колес
15.1 Технические характеристики и данные
15.2 Общие сведения
15.3 Ступица переднего колеса
15.4 Приводной вал
15.5 Ремонт приводных валов
15.6 Проверка и регулировка углов установки передних колес
15.7 Передняя стойка в сборе
15.8 Ремонт стойки передней подвески
15.9 Нижний рычаг передней подвески
16. Задняя подвеска
16.0 Задняя подвеска
16.1 Технические характеристики и данные
16.2 Общие сведения
16.3 Ступица заднего колеса
16.4 Проверка и регулировка углов установки задних колес
16.5 Корректирующий, верхний и нижний рычаги задней подвески
16.6 Замена втулки нижнего рычага
16.7 Продольный рычаг задней подвески
16.8 Задняя стойка
16.9 Ремонт задней стойки
17. Кузов
17.0 Кузов
17.1 Технические данные
17.2 Общие сведения
17.3 Ремонт незначительных повреждений кузова
17.4 Ремонт значительных повреждений кузова
17.5 Переднее крыло
17.6 Лючок наливной горловины топливного бака
17.7 Замена ветрового стекла и неподвижных стекол
17.8 Регулировка положения установки двери
17.9 Регулировка при возникновении неисправностей в механизме стеклоподъемника
18. Система кондициони-рования воздуха система
18.0 Система кондициони-рования воздуха система
18.1 Технические характеристики и данные
18.2 Общие сведения
18.3 Меры безопасности
18.4 Поиск и устранение неисправностей
18.5 Шумы, возникающие при работе компрессора кондиционера
18.6 Проверка уровня хладагента через смотровое окно
18.7 Проверка электромагнитной муфты компрессора кондиционера
18.8 Проверка ресивера / осушителя
18.9 Работа с трубками, шлангами и их соединениями
19. Электрооборудование автомобиля
19.0 Электрооборудование автомобиля
19.1 Технические характеристики и данные
19.2 Общие сведения
19.3 Электрические цепи
19.4 Аккумуляторная батарея
19.5 Выключатель зажигания и иммобилайзер
19.6 Метод регистрации идентификационного кода (ID)
19.7 Проверка датчика уровня топлива
19.8 Проверка датчика температуры охлаждающей жидкости
19.9 Комбинация приборов
20. Электросхемы
20.0 Электросхемы
automend.ru